For silver-based positive offset plates
Photomeg chemical system is designed for processing silver-based positive offset plates such as Itek Corporation’s Mega* plate, Mitsubishi’s Silver Master*, AGFA’s Setprint* and Supermaster*.
HOW PHOTOMEG SOLUTIONS ARE USED
Photomeg Activator Concentrate is diluted 1+1 with water (1 gallon of concentrate makes 2 gallons of working strength solution). Tank capacity on the more common camera-processors is 4 gallons of working strength solution, hence 2 gallons of concentrate are needed for start up. Another 4 gallons of working strength solution will usually be consumed through replenishment over the normal run length of a batch of chemistry.
Photomeg Stabilizer Concentrate is diluted 1+3 with water (1 gallon of concentrate makes 4 gallons of working strength stabilizer). Thus only 1 gallon of concentrate is needed for start up. Something less than 4 gallons of working strength stabilizer will be consumed through replenishment over the normal run length of the batch of chemistry.
Photomeg Plate Etch is used full strength, and is applied by means of a cotton pad to the whole plate surface. Only a small quantity is needed, but is should be applied uniformly over the whole area. The etch should be applied as soon as possible after the plate leaves the processor.
Photomeg 220 Fountain Solution Concentrate dilutes 1+7 with water (1 gallon of concentrate makes 8 gallons of working strength fountain solution). It is used in the normal manner for fountain solutions.
OPERATING TEMPERATURE FOR PHOTOMEG DEVELOPER
The developer tank should be at 85o F, although some latitude exists for operation in the range 80o~90o F. At 85o F, the best control over plate quality is obtained. The AGFA plate is best activated at 90º F.
CHEMISTRY CAPACITY AND LIFE
One change of chemistry should process at least 1,000 square feet of plate material (usually about 500-600 plates). As the chemistry becomes more contaminated through the processing of fresh plate material, some adjustment of exposure will be necessary. The chemistry should be changed and the tanks cleaned after processing 1,000 square feet of plate material, or after four weeks, whichever comes first. Regular users report that larger numbers than these are practical with the Photomeg System.
REPLENISHMENT DURING OPERATION
The activator and the stabilizer tanks are replenished with their respective working strength solutions. The rate of replenishment is determined by the “chick feeder” system on the camera-processor. Make sure that liquid levels in the activator and stabilizer tanks are maintained at the full marks.
TYPICAL CAMERA EXPOSURE
Follow the recommendations of the manufacturer of the camera-processor. In an Itek a suggested starting exposure is 7 seconds at F11. In a modified MR412 camera from 3M Co. a suggested starting exposure is 16 seconds at F11.
USE OF PHOTOMEG PLATE ETCH
APPLY PHOTOMEG PLATE ETCH BY MEANS OF A COTTON PAD AS SOON AS POSSIBLE AFTER THE PLATE LEAVES THE PROCESSOR. APPLY SMOOTHLY AND EVENLY TO THE WHOLE PLATE BUT DO NOT RUB HARD.
Do not stack wet plates because this can cause blinding. Plates must be dry before stacking.
Photomeg Plate Etch dries quickly. If it dries too quickly for smooth, even application, add 1 part of Photomeg 220 Fountain Solution Concentrate to 5 parts of Photomeg Plate Etch, and use this mixture as the plate etch.
INK SELECTION
Lower tack inks (19 or below) are recommended for better run length. It is normal to get 6,000 to 10,000 impressions with low tack inks, but with high tack inks this figure may be lower.
1 Gallon
Sold in cases of 4
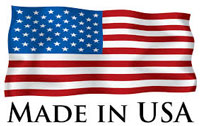